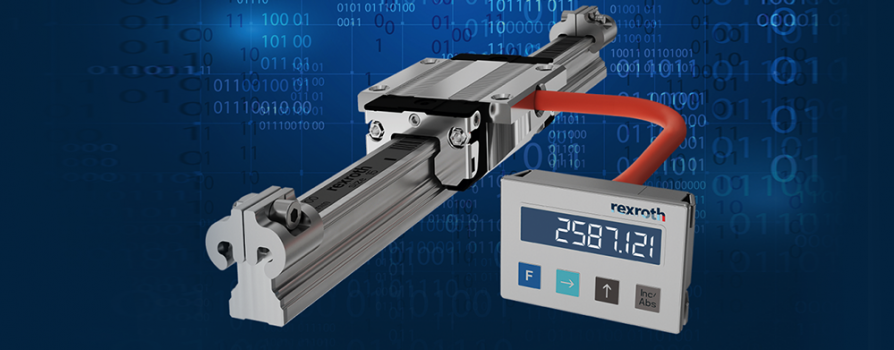
Integrated measuring systems are a robust and cost-effective alternative to externally mounted glass scales and linear encoders. We will tell you here why that is the case and how machines and users can benefit from them. Accuracy and dynamics are two main characteristics of machine tools and handling applications. Robust position measurement systems are needed to ensure that both characteristics are maintained over the long term. The problem is that they often suffer from the damaging impact of dust, oil, grease, shock and vibration. While short maintenance intervals maintain functionality, they also increase TCO. Would you like to learn about a robust and cost-effective alternative? Continue reading to learn more.
Tough, compact and connective.
The TruLaser 5000 fiber cutting units "fly" over the workpiece with twice the gravitational acceleration and travel speeds of up to 300 m/min. Despite these high dynamics, a glass scale is nowhere to be seen. Instead, the manufacturer Trumpf has opted for an integrated inductive measuring system (IMS) from Bosch Rexroth. The reason behind this: in tests with the fine dust that is deposited on the linear guides after laser cutting, the non-contact procedure demonstrated significantly higher strength and dynamics and required less maintenance. It is also built faster and more compact, since fewer parts and connection points have to be taken into account in the assembly process. This also increases ease of maintenance. For example, the slide block can be replaced independently of the measuring system. When necessary.
Broader application spectrum
The IMS required by Trumpf operates with a high accuracy of ± 4 μm with a repeat accuracy of ± 0.25 μm. Of course, there are also many engineering applications with less extreme requirements. For these cases, Bosch Rexroth has developed the IMScompact magnetic measuring system. This system is also contact-free, measures with ± 20 μm and a repeat accuracy of ± 1 μm and is available for measuring lengths up to 18 my ball-rail systems from size 15.
IMScompact: perfect for shafts with linear motors.
As with the inductive measuring system, the sensor for incremental and soon also for absolute measurement is completely integrated in the slide block of the IMScompact. Because its steel body functions as a Faraday cage, the magnetic measuring principle reliably provides exact values also in connection with linear motors. This EMV protection creates new opportunities for automation solutions in combination with linear motors. For example, the IMScompact is ideal as a position sensor on linear motor shafts and for increasing the position accuracy on belt drive shafts or shafts with ball screw assemblies. Externally mounted linear encoders become unnecessary.
Use alternatives, reduce engineering efforts
Inductive or magnetic, the IMS is ahead of other position measuring systems in many respects: the price advantage and reliability, the low maintenance of a non-contact and wear-free procedure and the reduced mounting and engineering efforts. This is because the dimensions of the guide block, apart from the IMScompact cable outlet or the measuring head mounted on the front of the IMS, are the same as those of standard blocks in roller rail systems and ball rail systems and can therefore be easily integrated into existing constructions.