The investment made for the acquisition of industrial machinery is very high and represents an important part of the assets of any company. Due to this significant investment, it is common for many manufacturers to continue operating with equipment and systems that have accumulated several years of service even though they are robust and reliable. Often, the performance of these machines remains optimal, meeting operational and production standards. However, this lengthy use brings with it the inevitable presence of parts and components that have become mechanically and technologically obsolete. Component obsolescence does not always mean that it is necessary to invest in new parts or purchase completely new machinery. In many cases, there is a more economical and sustainable alternative to extend the life of existing equipment and improve its performance.
In this post, we will explore in detail the retrofit process, analyze its different stages, the potential benefits of its implementation and how it could be an efficient and cost-effective solution for companies seeking to remain competitive and operational in a constantly dynamic environment.
Join us on this tour and discover how retrofit can transform your industrial operations!
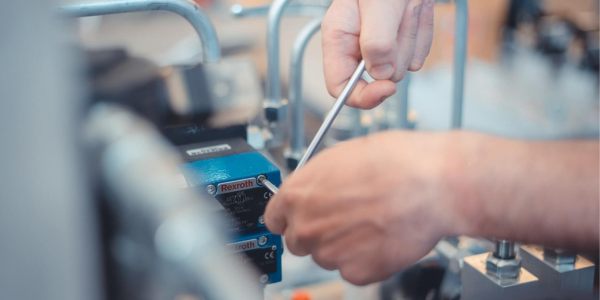
What is a retrofit?
Retrofit is the upgrading and modernization of obsolete controls and drives of a machine to increase performance, efficiency and safety. In other words, it is a process of renovation of components while maintaining the machine's base.
It contributes to the extension of the life cycle of your machinery by significantly reducing downtime and investment, as both the installation and purchase of new equipment involves very high costs. In many cases, the objective of a retrofit is to adapt to new production requirements, changes in the environment, upgrades, etc. Among the many benefits of a retrofit, we highlight the following:
Performance, energy efficiency and safety:
Safety is one of the most important aspects to consider in a factory and older machinery may lack up-to-date safety systems. With a retrofit you can bring your equipment up to the necessary safety requirements and standards. Moreover, by implementing advanced technologies, you align it with the new Industry 4.0 trends, focusing on improving productivity and promoting sustainable production.
Reduced costs and downtimes:
It is a more cost-effective alternative to purchasing new equipment. In addition, retrofit periods are shorter than installing new machinery.
Regulatory compliance:
Without the need to make a considerable investment in the acquisition of new equipment, it is possible to comply with current legal requirements and, at the same time, maintain a high level of competitiveness in the market.
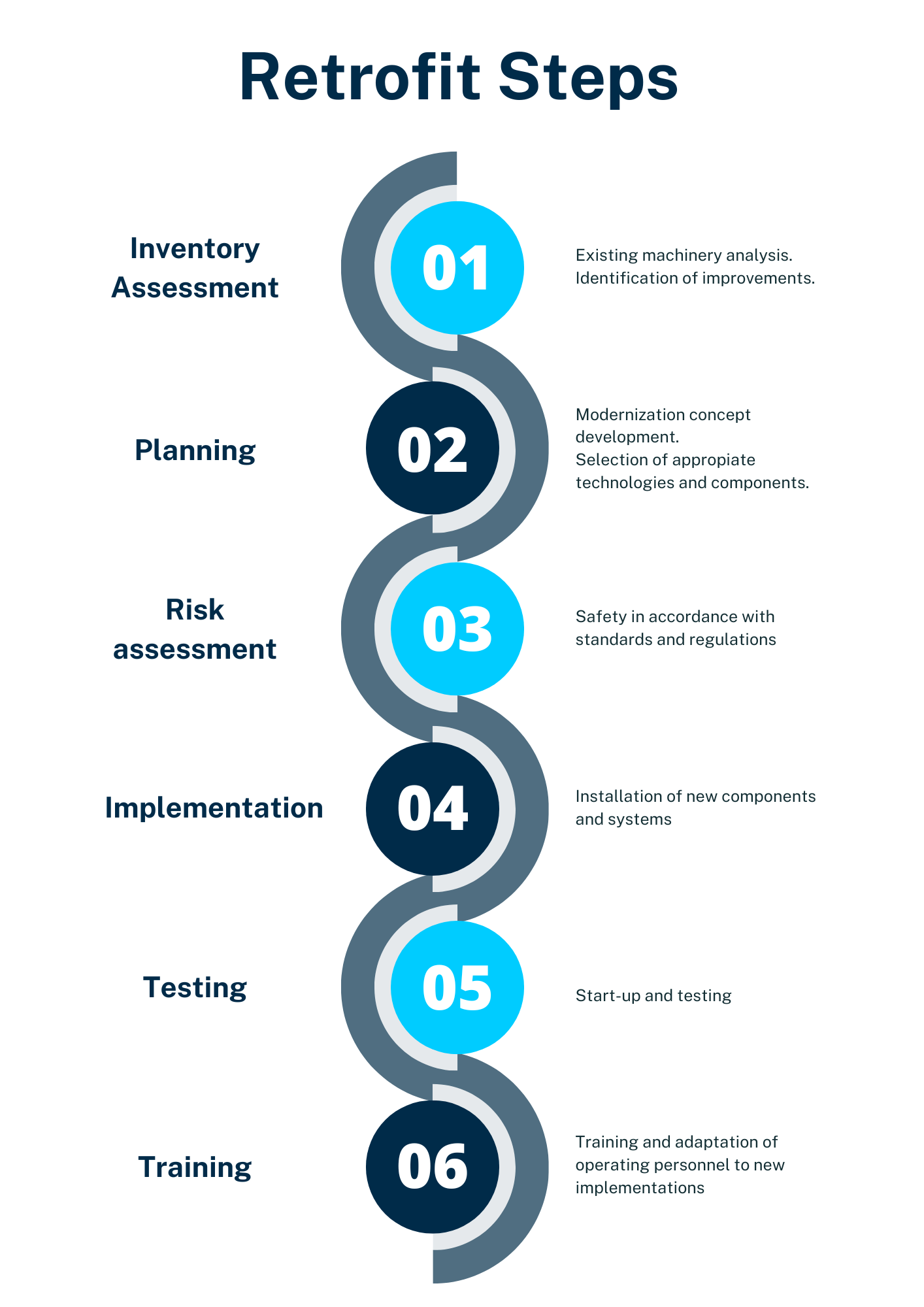
Retrofit process steps
Do you know how a retrofit is carried out? The retrofitting process has different phases. Before its execution, it is necessary to prepare and analyze different aspects that will be of vital importance for the evolution of the retrofit. Likewise, the retrofit does not end after the updating of the parts and components but requires subsequent phases.
Below, we tell you step by step.
Inventory assessment: Before to any direct action, the existing equipment must be analyzed and the obsolete or damaged components to be modernized must be identified in order to find an alternative and outline a strategy.
Planning: In each case different actions are carried out, so the retrofit concept in question is developed and the most appropriate components are selected in each case.
Risk assessment: The retrofit is developed in accordance with current regulations and a monitoring of the safety requirements is carried out with the aim of rectifying possible failures and outdatedness.
Implementation: This phase comprises the installation of the components and the integration of the new technology into the existing machine
Testing and commissioning: Several tests are performed to verify that the implementation phase has been successful before start-up.
Training:The relevant personnel involved in the changeover are instructed in the efficient use and utilization of the new machinery and components.
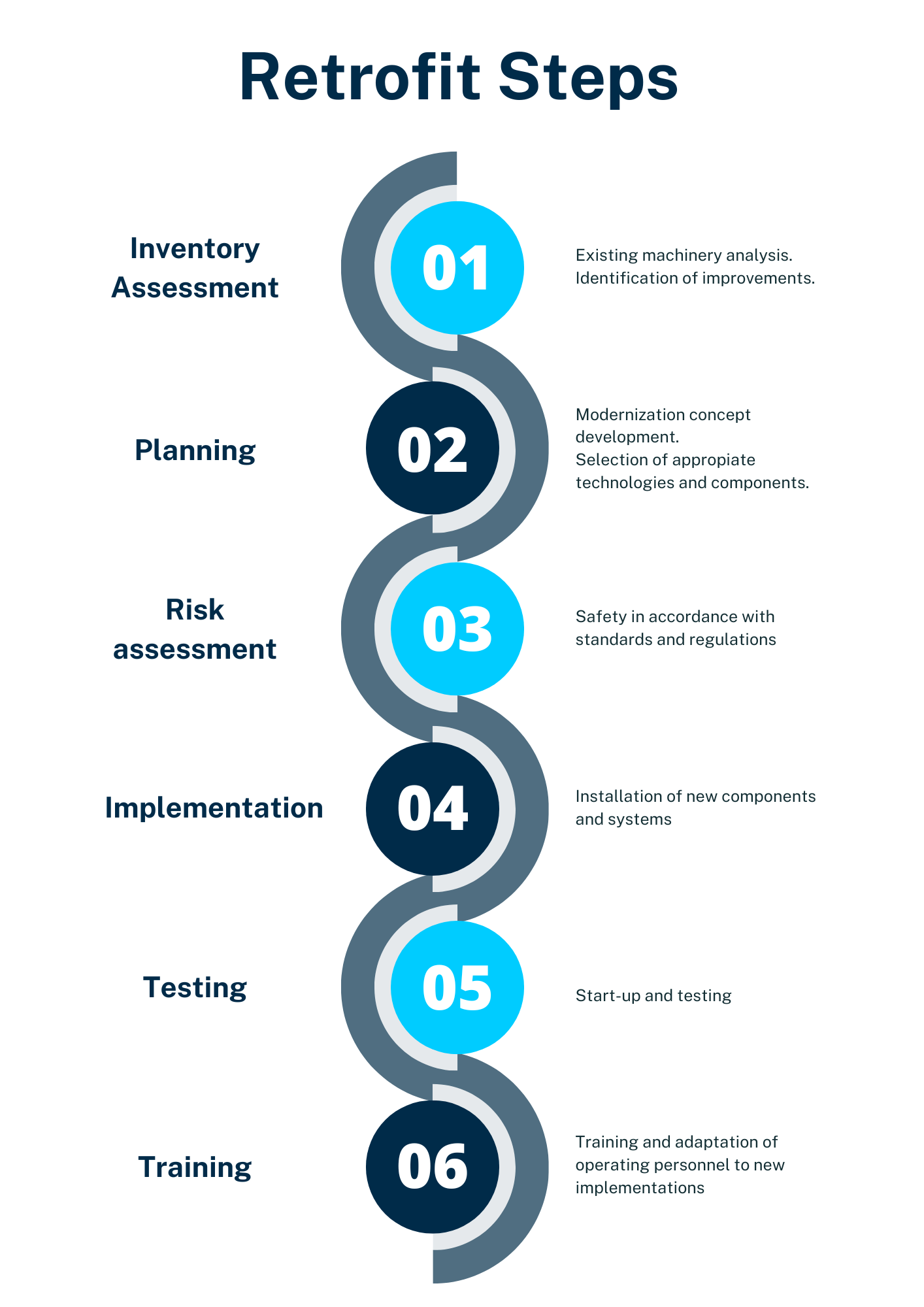
Retrofit process steps
Do you know how a retrofit is carried out? The retrofitting process has different phases. Before its execution, it is necessary to prepare and analyze different aspects that will be of vital importance for the evolution of the retrofit. Likewise, the retrofit does not end after the updating of the parts and components but requires subsequent phases.
Below, we tell you step by step.
Inventory assessment: Before to any direct action, the existing equipment must be analyzed and the obsolete or damaged components to be modernized must be identified in order to find an alternative and outline a strategy.
Planning: In each case different actions are carried out, so the retrofit concept in question is developed and the most appropriate components are selected in each case.
Risk assessment: The retrofit is developed in accordance with current regulations and a monitoring of the safety requirements is carried out with the aim of rectifying possible failures and outdatedness.
Implementation: This phase comprises the installation of the components and the integration of the new technology into the existing machine
Testing and commissioning: Several tests are performed to verify that the implementation phase has been successful before start-up.
Training:The relevant personnel involved in the changeover are instructed in the efficient use and utilization of the new machinery and components.
To avoid uncomfortable situations and unsatisfactory results, we recommend that you work directly with the manufacturer (if they have a Retrofitting service) or, if applicable, with a partner.
What are the advantages of working with the official technical service?
- Use of original components
- Qualified personnel with many years of experience
- Complete functional tests
- Compliance with Testing standards (Atex, UL, CE, Safety, etc)
- Possibility to request configuration modifications (brake changes, encoder, connector orientations, etc)
- Guaranteed process
- Detailed reports
After all, these types of operations are based on the mutual trust of the companies and professionals involved. The stakes are high in this type of process. Therefore, commitment at every stage is essential to obtain a satisfactory result.